Why Ignoring Your Facility’s Data Backup Plan Could Be a Costly Mistake
April 4th, 2025
4 min read
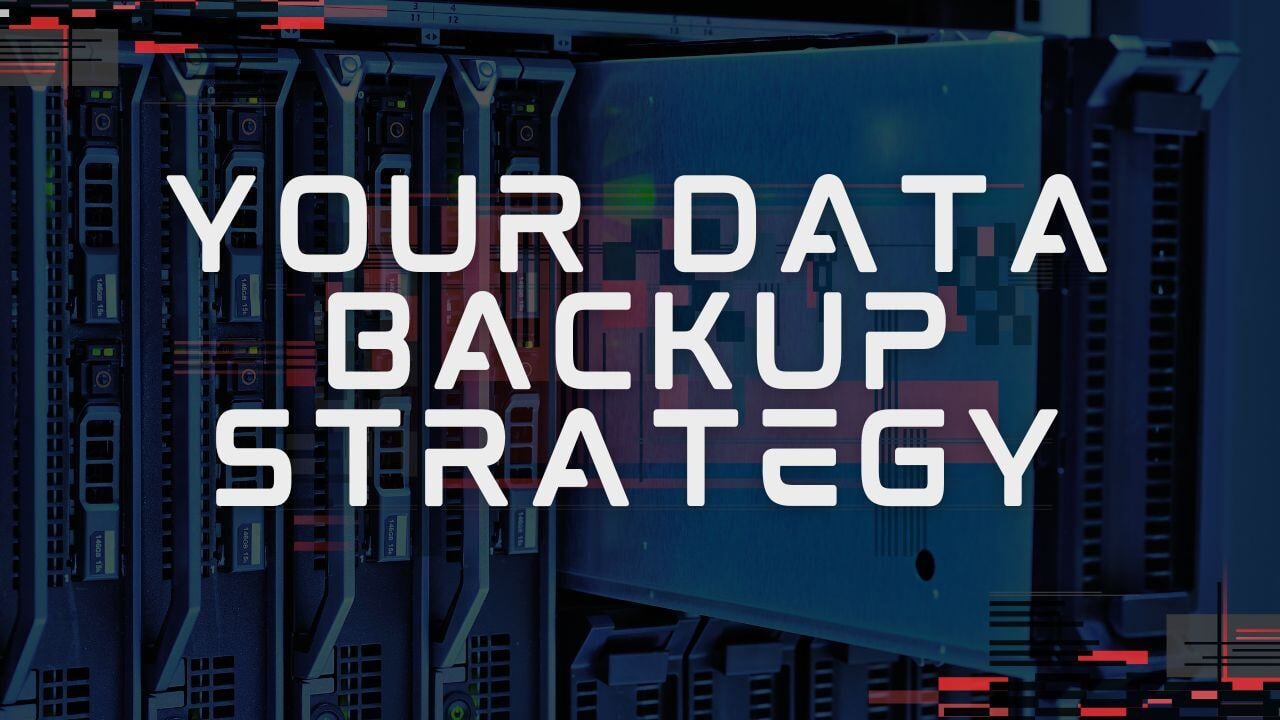
In industrial automation, we spend a lot of time focused on what we can see: the flashing indicators on your HMI, the hum of motors, the precise rhythm of a well-configured drive. But behind all of that hardware is something less visible and far more critical. It’s data. And when that data isn’t backed up or protected, all those perfectly running systems can grind to a halt in seconds.
At HESCO, we’ve worked with manufacturers who’ve seen the impact firsthand. Whether it’s a corrupted PLC, a ransomware attack, or a failed historian server, one thing is clear: without a solid backup strategy, recovery becomes slow, expensive, and sometimes impossible.
So why is backup still treated like a “maybe someday” project in so many facilities? And what will it take for teams to see it for what it truly is: one of the most important safety nets your operation can have?
The Hidden Weak Spot in Too Many Facilities
When backup isn't part of your day-to-day operational thinking, it’s easy to fall into the trap of assuming things will always “just work.” But all it takes is one power surge, one hardware failure, or one employee clicking the wrong email for that illusion to fall apart.
And in automation, “just a little downtime” doesn’t exist. A lost PLC program isn’t just a software issue, it’s a production line offline. It’s orders unfulfilled. It’s staff standing around waiting. It’s your maintenance team scrambling to recover something that might not be recoverable at all.
The reality is, your logic files, historical data, trending reports, recipes, and configurations are your operation. They’re not just support systems. They’re the foundation everything else is built on. Lose them, and you’re not just repairing equipment; you’re rebuilding your knowledge base from the ground up.
The Real Costs of Doing Nothing
Think about the last time your team lost even an hour to troubleshooting or recovery. Now multiply that by eight hours. Maybe twelve. Maybe seventy-two. That’s the kind of delay a single failed drive or unprotected HMI can create if there’s no viable backup.
Worse, many manufacturers discover their data is gone for good. Whether it’s a file that wasn’t properly saved or a ransomware attack that encrypted everything on-site, that data is often irreplaceable. More than downtime, it’s lost intellectual property, lost configuration knowledge, and sometimes, lost customer trust.
And if your facility operates in a regulated environment, you could be on the hook for even more. Imagine being audited and not having access to your compliance logs or quality data. Fines and certification issues are very real outcomes, and they’re entirely preventable.
The financial impact adds up fast. Between lost production time, emergency IT support, parts replacement, and penalty fees, a single failure could cost tens or even hundreds of thousands of dollars. For some small to mid-sized facilities, it could jeopardize an entire quarter, or worse.
Ransomware Isn’t Just an IT Problem Anymore
In recent years, the cybersecurity threat landscape has shifted. What used to be limited to enterprise networks and email servers is now targeting the plant floor. Ransomware has found its way into OT environments, locking down PLCs, drives, and other essential systems.
These attacks are sophisticated and increasingly automated. And while air-gapped systems used to provide a buffer, modern connected facilities can’t always rely on isolation to stay safe.
If your only copy of operational data lives on the device that just got encrypted, your options narrow fast. But if you’ve been backing up regularly and storing those backups offsite or in the cloud, you can be back up and running in a fraction of the time.
One of the most overlooked aspects of ransomware protection is timing. A system that gets encrypted mid-shift could cause not just data loss, but safety hazards, product waste, or even physical equipment damage, depending on the process interrupted. With clean backups, you regain control quickly and safely.
Backing Up Is Easier Than You Think–If You Do It Intentionally
Creating a backup strategy doesn’t have to be overwhelming. The key is to be deliberate and consistent. Start by identifying what actually needs to be protected: PLC programs, HMI configurations, historian data, even your network switch settings. You’d be surprised how often those “support files” are overlooked until you need them.
Next, determine where your data lives and how critical each system is to daily operations. Some systems will require real-time backups; others can get by with weekly snapshots. Understanding that mix helps you prioritize your resources without overengineering the solution.
And while backup software is important, it’s only part of the equation. You also need the right storage infrastructure, whether that’s an on-site appliance for fast restores or a cloud-based solution for disaster recovery. Redundancy is non-negotiable. If your backup only lives in one place, you’re still one event away from data loss.
The good news? More tools than ever before are designed specifically for industrial environments. You no longer have to rely on consumer-grade systems or shoehorn in IT tools that don’t understand PLCs and OT architecture.
Redundancy Isn’t Paranoia, It’s Planning
Let’s say you’ve got your backups running on a server down the hall from your control room. That’s great, but what happens when that part of the building floods or experiences a surge? That’s why every serious backup strategy includes multiple layers.
Storing copies in another facility or using a cloud provider with encrypted, industrial-grade storage gives you options when things go wrong. And when it comes to ransomware, having a secure, isolated, or even immutable backup can mean the difference between a fast recovery and a week of chaos.
If you’re unsure whether your backups are protected from internal threats, such as accidental deletion or disgruntled insiders, then isolation strategies (like offline backups or WORM drives) are something to consider seriously. These aren't just IT buzzwords, they're lifesavers in critical moments.
And Yes, You Have to Test
This is the part no one wants to hear, but it’s the most important: if you haven’t tested your backups, they don’t count. Maybe the file was saved incorrectly. Maybe the firmware changed and now won’t re-import. Maybe the technician skipped a step three months ago. You won’t know until it’s too late; that is, unless you test regularly.
That means restoring a drive, uploading a PLC file, simulating a failure, and verifying that everything still works. Testing may feel like a chore, but it gives your team confidence when the pressure’s on. It’s how you turn a “maybe” recovery into a guaranteed one.
Don’t Let One Oversight Define Your Next Crisis
At the end of the day, a good backup strategy isn’t about technology, it’s about risk management. It’s about making sure that one bad day doesn’t spiral into lost weeks, lost contracts, or lost reputation.
If your team isn’t sure where the backups are, or when they were last tested, or if they even exist in the first place, it’s time to fix that.
And the best time to start? Before something breaks.
At HESCO, we help manufacturers build backup strategies that match the complexity and criticality of their operations. Whether you're starting from zero or looking to modernize what you’ve already got, we’ll help you identify vulnerabilities, recommend tools that work for your setup, and ensure your data stays protected, no matter what hits you next.
Talk to us today and let’s get you out of the danger zone and into the safety net your facility deserves.