5 Critical Reasons to Perform an Installed Base Evaluation (IBE)
March 21st, 2025
4 min read
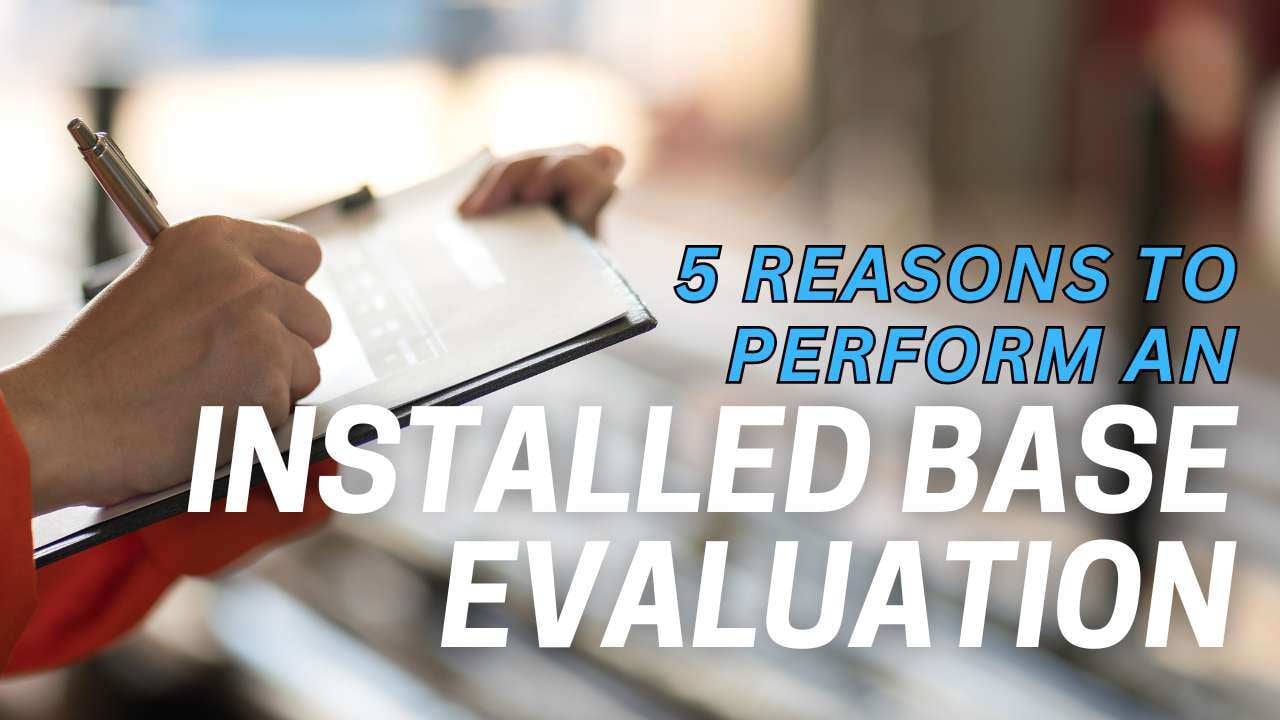
If you manage maintenance, engineering, or operations at a manufacturing facility, you already know how much rides on the health of your automation assets. But when was the last time you had a clear, accurate, and up-to-date picture of exactly what hardware is installed across your plant?
If your answer is somewhere between “it’s been a while” and “I’m not sure we’ve ever done that,” you’re not alone. This is precisely why an Installed Base Evaluation (IBE) is one of the smartest investments you can make for your facility.
At HESCO, we’ve worked with manufacturers across industries to perform these evaluations, and the benefits are clear: lower risk of unplanned downtime, smarter storeroom management, and more predictable capital planning. Whether you’re running aging legacy systems or cutting-edge automation, the insights from an IBE pay dividends almost immediately.
Here are the top five reasons why an IBE deserves a spot on your 2025 maintenance calendar, and how this proactive step can help your facility avoid some extremely costly mistakes.
What is an Installed Base Evaluation (IBE)?
Before we dive into why you should schedule an IBE, let’s briefly cover what it actually is and why it matters.
An Installed Base Evaluation is a comprehensive audit of your facility’s automation assets. This isn’t just a quick walk-through with a clipboard. It’s a structured process, typically performed by authorized distributors like HESCO, that combines onsite data collection, condition assessments, and lifecycle analysis to create a complete picture of your plant’s automation health.
Every piece of hardware, from PLCs and drives to HMIs and power supplies, is documented, along with its location and lifecycle status (active, active-mature, end-of-life, or discontinued). Your spare parts inventory is cross-checked to see what you have, what you’re missing, and what you no longer need.
The end result isn’t just data; it’s an actionable roadmap that helps you reduce unplanned downtime, improve spare parts management, and plan future upgrades with confidence.
1. You’ll Finally Have a Map of All Your Critical Control Hardware And Where It Lives
Ask yourself this: if a drive or PLC failed tomorrow, how quickly could your team find and access that specific device? In many plants, control hardware has been added over decades, sometimes during emergency projects, plant expansions, or equipment upgrades. The result? Devices scattered across your facility, with no single source of truth for where everything is located.
An IBE gives you that missing map. During the onsite evaluation, trained experts walk your entire facility, documenting every piece of control hardware, from large PLC racks to small operator terminals. This isn’t just a high-level list — it’s a detailed panel-by-panel accounting of where each critical asset is physically installed.
Why does that matter? When something goes wrong, time spent searching is time lost. With an IBE report in hand, your team can go straight to the problem, shortening both troubleshooting time and downtime. That single benefit alone can make an IBE worth the investment.
2. You’ll Uncover Any Gaps in Your Spare Parts Inventory
If you’ve ever had a machine go down only to realize you don’t have the critical spare part needed to fix it, you understand the frustration — and the financial pain — that comes with it.
One of the most valuable outputs of an IBE is the spare parts analysis. Once your installed hardware is documented, that data is cross-referenced with your existing spare parts inventory. This process flags missing, outdated, or inaccurately tracked spares — giving you a clear, prioritized list of what to order to shore up your storeroom.
This is especially important for facilities that have gone through staffing changes, expansions, or system upgrades over the years. It’s common to assume you have a spare on the shelf, only to find out during a failure that you don’t — or that the spare you do have isn’t compatible with your current system.
The IBE process helps you correct these gaps before they cause downtime. It also gives your purchasing team the data they need to build a smarter stocking strategy, focusing on the parts that truly matter for uptime.
3. It’s a Perfect Opportunity to Clean Out Excess and Inactive Spares
Most storerooms don’t just suffer from missing parts–they’re also packed with outdated, obsolete, and excess inventory. Over time, as equipment gets upgraded or replaced, spares that once made sense become unnecessary clutter.
An IBE doesn’t just help you identify what you need; it also highlights what you don’t. That means you can free up valuable storeroom space, eliminate waste, and even recapture working capital by offloading unused inventory.
We’ve seen facilities discover tens of thousands of dollars worth of obsolete parts during an IBE, allowing them to free up shelf space to create a cleaner, more organized storeroom. This level of visibility makes your entire maintenance operation leaner, faster, and more cost-effective.
4. You’ll Finally See Where Your Facility is Most Vulnerable to Aging and Obsolescence
Automation technology changes fast. Devices that were state-of-the-art 15 years ago could now be obsolete, with no direct replacements or repair services available.
One key deliverable from an IBE is a full lifecycle status report for every asset you own. Each device is classified as either active, active-mature, end-of-life, or discontinued. This is where the evaluation becomes a powerful risk management tool.
Knowing which assets are no longer supported (or will soon lose support) allows you to build a proactive upgrade plan, rather than scrambling during a failure. Instead of emergency spending and production disruptions, you can budget and schedule upgrades on your terms.
This is especially important for facilities running legacy Rockwell Automation hardware (like PLC-5 or SLC 500 systems) or discontinued drives. In today’s supply chain climate, sourcing discontinued parts is difficult and expensive, if they can be found at all. The IBE gives you the foresight to plan ahead, reducing both risk and cost.
5. You’ll Walk Away with Actionable Insights, Not Just a Spreadsheet
The real power of an IBE comes after the site visit when the data is analyzed and turned into a clear action plan for your facility.
That action plan goes beyond a simple inventory list. It connects the dots between your hardware, your storeroom, your risks, and your future maintenance spending.
The final IBE report will include:
- Identification of critical spares missing from your storeroom, leading to less downtime
- Identification of high-risk legacy hardware with recommendations ranging from supporting existing hardware to modernization paths
- Opportunities to consolidate and standardize platforms to simplify future maintenance and reduce the total number of spares in your storeroom
- Recommendations to improve safety (such as ensuring proper Arc Flash labeling)
- Recommendations on how to achieve a more predictable and stable maintenance spend
In short, an IBE doesn’t just answer, “What do we have?” It answers, “What should we do about it?”
The Bottom Line: Predictability is Priceless
Whether your facility is large or small, old or new, one thing is true: unplanned downtime is expensive. Studies show that unplanned downtime costs industrial manufacturers an estimated $50 billion a year. Even in smaller operations, avoiding just an hour or two of downtime will more than cover the cost of an IBE.
An Installed Base Evaluation isn’t just a smart maintenance tool, it’s a smart business decision. It’s about shifting from reactive firefighting to proactive planning, where you control your maintenance budget instead of being controlled by it.
If you haven’t performed an IBE in the last five years (or ever), now is the time. Technology moves fast, and the longer you wait, the harder it becomes to catch up. Ready to schedule your IBE? Reach out to HESCO today.