Repairs vs. Remanufacturing: A Simple Fix or an Investment in Reliability?
April 9th, 2025
4 min read
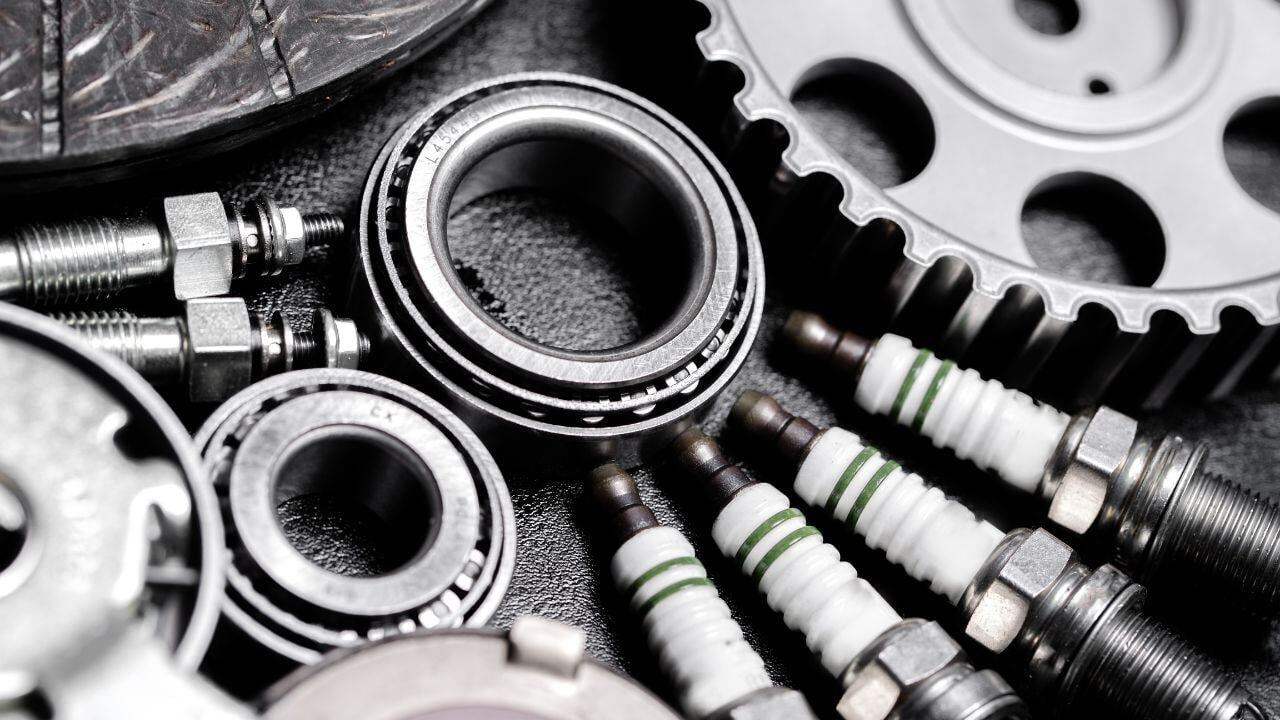
It’s an inevitable scenario—one day, a critical piece of equipment in your facility breaks down, bringing everything to a standstill. You need a plan. Without one, you’re left scrambling, hoping you can get it fixed before downtime costs spiral out of control.
This is where a solid repair management strategy makes all the difference. When a system fails, you want to know exactly how you’re going to fix it, who’s going to handle the job, and how long you can expect it to last once it’s back up and running. The right strategy doesn’t just get you operational again—it helps you control costs, maximize uptime, and prevent repeat failures.
But here’s where many companies get stuck: should you opt for a quick repair, or is remanufacturing the better choice? The answer isn’t always obvious, but if you’re looking for long-term reliability and cost savings, remanufacturing is often the smarter move.
Here at HESCO, we have over eight decades of experience in industrial automation. We have helped our customers with repairs and remanufacturing for a variety of parts. In this article, we’ll discuss the importance of having a repair management strategy and when it’s smarter to choose repairing or remanufacturing.
Why Your Repair Strategy Matters
Imagine your car’s check engine light comes on. Would you immediately head to the dealership and buy a brand-new vehicle? Probably not. You’d diagnose the issue and replace only what’s needed. Now, let’s take that analogy a step further. What if it’s not the engine light but a flat tire? Would you replace just the tire, or scrap the entire car?
In industrial settings, the same logic applies. When a component fails, some companies default to full replacements, assuming it’s the safest choice. Others opt for quick repairs, fixing only the immediate issue. But without a strategy, both approaches can become expensive in the long run.
A well-planned approach to maintenance, repair, and operations (MRO) is about more than reacting when things break. It’s about knowing in advance how failures will be handled, ensuring your systems are running as efficiently as possible, and, ultimately, making the best financial decision for your operation.
What a Strong Repair Management Strategy Looks Like
A good repair management strategy isn’t just about fixing things when they break—it’s about controlling costs, reducing risk, and ensuring long-term reliability. Here’s what that looks like in practice:
- Predictive and Preventive Maintenance: Instead of waiting for failures to happen, leading companies use predictive maintenance to monitor equipment health. Sensors, software, and historical failure data can identify potential issues before they cause a breakdown. Preventive maintenance schedules routine inspections and part replacements to avoid unnecessary downtime. Investing in these technologies helps businesses avoid emergency failures altogether.
- Inventory Control: Knowing which spare parts you need and keeping them in stock can mean the difference between a one-hour fix and a multi-day shutdown while waiting for a shipment. Smart inventory management ensures you have critical components available without overstocking parts you rarely use.
- Standardized Processes: A structured approach ensures that repairs are performed consistently and correctly. Having clear guidelines on when to repair, when to remanufacture, and when to replace reduces last-minute guesswork and prevents unnecessary spending.
- Trusted Repair and Remanufacturing Partners: Not all repairs are equal. Working with an OEM or an authorized remanufacturer ensures that your equipment is restored to the highest possible standard. A bad repair job from an unreliable third party can lead to premature failures and costly repeat work.
- Cost-Benefit Analysis: Every failure presents a financial decision. A well-planned repair strategy includes a framework for evaluating repair costs versus replacement costs—factoring in things like downtime, expected lifespan, and total cost of ownership.
Repair vs. Remanufacturing: What’s the Difference?
At its core, repair is about restoring function. A technician identifies what’s broken, replaces or fixes the damaged component, and sends the unit back into service. The problem is, that’s often where it ends. Most third-party repair shops will address only the specific failure without looking at the bigger picture. Other parts of the unit may already be deteriorating, and without a full inspection, you’re simply resetting the clock until the next failure.
Remanufacturing, on the other hand, is a full-system reset. Instead of just replacing the failed component, the unit is completely disassembled, cleaned, inspected, and rebuilt. Every worn or aging part is replaced, not just the one that caused the failure. That means when the unit is returned, it’s in like-new condition—not just functional, but restored to its original performance specifications or better.
The Financial and Operational Impact of Remanufacturing
At first glance, a basic repair might seem like the cheaper option. If you only fix what’s broken, you’re only paying for that one part. But what happens when another component—one that was already close to failure—gives out a few months later? You’re right back where you started, paying for another repair, dealing with more downtime, and inching closer to what a full replacement would have cost in the first place.
With remanufacturing, you get a unit that’s been fully rebuilt to perform like new. That means fewer unexpected failures, fewer emergency shutdowns, and a longer overall lifespan. Instead of playing whack-a-mole with repairs, you’re making a one-time investment that keeps your operation running smoothly.
How Downtime Eats Into Your Bottom Line
Every hour of downtime costs you. Whether it’s lost production, wasted labor, or unfulfilled customer orders, the financial impact of equipment failure can be staggering. According to industry research, unplanned downtime costs manufacturers an average of $50 billion a year.
Let that sink in. Every minute your facility isn’t running, you’re bleeding revenue. If a quick repair means you’ll be facing another failure in six months, was it really the cheaper option? Or are you just kicking the can down the road?
This is why remanufacturing is a long-term cost control strategy, not just a maintenance decision. Instead of reacting to each failure individually, you’re making sure your equipment runs reliably for years, not just weeks or months.
A More Sustainable Approach to Equipment Management
Beyond cost savings and reliability, remanufacturing also aligns with sustainability initiatives. By reusing existing components, you’re reducing waste, lowering material consumption, and minimizing your operation’s environmental footprint. Instead of discarding failed equipment, you’re giving it a second life—while ensuring it performs just as well as a brand-new unit.
For companies prioritizing corporate sustainability goals, remanufacturing isn’t just a financial win—it’s a responsible business practice that contributes to reduced industrial waste and energy conservation.
Make the Right Choice for Your Facility
The next time a piece of equipment fails, take a step back before opting for a quick repair. Ask yourself:
- How often has this unit needed service in the past?
- Would remanufacturing extend its service life and prevent future failures?
- Am I saving money in the short term only to spend more in the long run?
There’s a time and place for quick fixes, but when reliability, cost-effectiveness, and long-term performance matter, remanufacturing is often the better choice. It’s not just about fixing what’s broken—it’s about ensuring your equipment runs better, longer, and smarter so you can focus on keeping your operations efficient and profitable.
If you’re in need of repair or remanufacturing services or want more tips on how to craft a repair management strategy that’s right for your facility, contact us at HESCO. We’d be happy to help you with next steps to make sure your parts are running smoothly and efficiently.