Time to Modernize Your Facility? Why You Can’t Afford to Wait
May 8th, 2025
4 min read
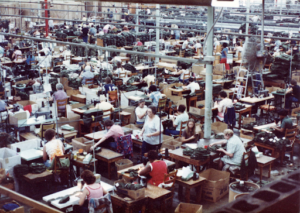
If your facility is still running on legacy equipment and outdated automation systems, you’re not alone. Plenty of manufacturers are asking the same question: “If it’s still working, why change it?”
But in today’s fast-paced industrial landscape, standing still is the same as falling behind. Technology is advancing at a rapid rate, and with each generation of hardware and software, manufacturers who modernize are gaining advantages in efficiency, safety, and operational cost.
At HESCO, we’ve spent over 85 years helping facilities evolve. And we can confidently say: modernization isn’t about chasing the newest gadget. It’s about future-proofing your operations in ways that directly impact your bottom line.
Here’s what modernization really means, why it’s more essential than ever, and how to start making smart, strategic updates without disrupting your operation.
What Modernization Really Means
Facility modernization is not a one-size-fits-all process. For one operation, it may mean replacing a decades-old PLC that’s been running nonstop since the 1990s. For another, it could be switching to drives that are safer, more compact, and energy efficient. The goal is simple: replace what’s no longer serving you and equip your team with systems that reduce risk and improve output.
Modernization can include everything from updating firmware to migrating entire control systems. But it doesn’t have to be overwhelming. When done strategically, it helps your team work smarter and prepares your operation for long-term success.
Think of it like replacing a rotary phone with a smartphone. You can still make calls either way, but one gives you far more functionality, flexibility, and security.
Why Manufacturers Delay, and Why That’s Costly
We hear it all the time: “The old system is still running fine.” That might be true today. But what about when it fails tomorrow?
For example, one HESCO customer was running a legacy control system on a packaging line. Everything seemed fine until one of the processors failed. The replacement part? Discontinued. Their only option was to source a refurbished unit from a third-party seller, at four times the original cost and with no warranty. The system was down for four full days while waiting for a workaround.
This story isn’t unique. It’s a preview of what can happen when aging infrastructure is pushed too far. Modernization isn’t about fixing what’s broken; it’s about ensuring the most important parts of your facility never break at the wrong time.
The Hidden Costs of Not Modernizing
The decision to delay modernization is rarely about risk, it’s about cost. But often, the cost of not modernizing is far greater than expected. Let’s look at what that means.
Cost of Maintenance and Downtime
Older machines require more frequent repairs and often have fewer available parts. As OEMs discontinue support, replacement parts become harder to find, more expensive, and slower to deliver. Downtime can stretch from hours to days, especially when the right part is sitting in someone else's warehouse across the country.
And when that older equipment fails, it’s rarely an isolated issue. A single control board failure can cascade through systems, shutting down multiple processes and forcing reactive fixes that don’t always stick.
Increased Energy Bills
Many older systems operate with low efficiency, particularly when it comes to motors, drives, and lighting. You might not notice it month to month, but when you step back and audit total energy usage, the savings from newer, energy-efficient components become clear.
In facilities we’ve assessed, we’ve seen energy consumption drop by as much as 20% simply by upgrading key pieces of automation equipment. Over the course of a year, that kind of efficiency pays for itself.
Cybersecurity Risks
Modern threats require modern defenses. Legacy PLCs, HMIs, and unmanaged switches often lack the built-in protections today’s manufacturing environment demands. In a world where ransomware is now a real threat on the plant floor, outdated systems leave you vulnerable.
Cybercriminals don’t care how old your equipment is, they care how easy it is to exploit. And unsecured, out-of-date hardware is the easiest entry point they can find.
How to Modernize Strategically (Without Shutting Down Your Facility)
Modernization doesn’t have to mean ripping out entire lines or buying all new equipment at once. At HESCO, we guide customers through phased modernization strategies built around the concept of prioritized risk.
We start with an Installed Base Evaluation (IBE), which gives you a full audit of your hardware, firmware, lifecycle status, and support risks. From there, we identify the biggest risks to your productivity: maybe it's an aging PLC series, or a communications network that's held together by firmware workarounds and luck.
Then, we help you plan a roadmap: which equipment can stay, which needs upgrading, and how to roll those changes out in a way that aligns with your budget and minimizes downtime. Think of it as “retrofitting with intent”—we help you modernize where it counts most.
One customer recently used this approach to migrate from SLC 500 controllers to CompactLogix over a two-year window, one line at a time. Not only did they avoid large-scale disruption, but they also saw reduced downtime and energy use within six months of the first phase going live.
Modernization Isn’t Just Necessary, It’s Profitable
While some modernization decisions may be driven by risk (safety, obsolescence, cybersecurity), others offer clear financial benefits.
When you reduce unplanned downtime, extend equipment lifespan, lower energy usage, and improve cycle times, those gains show up quickly on the bottom line. What seems like a capital expense today is actually a lever for long-term cost control.
Facilities that modernize also position themselves for future integration: digital twins, IIoT analytics, remote diagnostics, and AI-driven optimization all start with a foundation of modern, connected equipment.
Where HESCO Fits In
We’re not just here to sell hardware. We’re here to help you build a modernization strategy that’s realistic, data-driven, and tailored to your facility’s needs. We do that through:
- Installed Base Evaluations: to inventory what you have and identify hidden risks.
- Lifecycle Reporting: to show which assets are aging out or unsupported.
- Strategic Planning: to help you modernize in phases—without overextending your budget or disrupting production.
We also educate your team so you’re not just upgrading technology, you’re building internal confidence and capability along the way.
The Bottom Line? It’s Time to Modernize
If you’re still running systems that haven’t changed in a decade or more, now is the time to take action. The cost of waiting is rising, and the benefits of updating have never been greater.
Modernization protects your uptime, your people, and your profits. And with the right plan, it’s not disruptive. It’s transformative.
Let’s talk about what’s next for your facility. Contact HESCO today to schedule your Installed Base Evaluation and start building your modernization strategy.